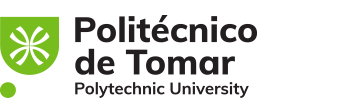
Publication in the Diário da República: Despacho n.º 10852/2016 - 05/09/2016
4 ECTS; 3º Ano, 1º Semestre, 15,0 T + 30,0 PL + 2,0 OT , Cód. 938069.
Lecturer
- Fernando dos Santos Antunes (1)(2)
(1) Docente Responsável
(2) Docente que lecciona
Prerequisites
Not applicable.
Objectives
1. Know the technology of carving and furniture - materials, techniques and technological means of artistic production of carving and furniture;
2. Identify and understand wooden structures the art and technique of producing connection and fitting systems;
3. Understand and execute decorative ornamental and figurative techniques the art and technique of carving or carving wood;
4. Understand and execute decorative coatings with metallic foil and polychrome the art and technique of gilding and silvering, and the art and technique of polychrome on metallic coatings;
5. Understand and execute decorative techniques on furniture the art and technique of decorating and covering wood, the art and technique of coloring wood, and the art and technique of finishing and polishing wood.
Program
A. BRIEF INTRODUCTION TO OF WOODCARVING AND FURNITURE TECHNOLOGY
1. Main materials and products used in artistic production of the of timber artifacts
2. Terminology used in woodworking area
3. The Wood Workshop
3.1. Main equipment, tools and instruments
3.2. Basic hygiene rules, health, safety and organization
B. WOOD STRUCTURES ASSEMBLAGE AND JOINERY SYSTEMS
1. Art and technique of the assemblage and joinery in wood structures
1.1. Selection and preparation of wood
1.2. Measurement
1.3. Draw cutting lines
1.4. Cutting and setting
1.5. Gluing and clamping techniques
C. ORNAMENTAL AND FIGURATIVE DECORATIVE TECHNIQUES
1. Art and technique of carving or sculpting wood objects
1.1. Execution of drawing or sketch and auxiliary markings
1.2. The selection and preparation of wood
1.3. Transposition of the drawing
1.4. Cut out the contours
1.5. Wood thinning
1.6. Modelling of volumes
1.6.1. Thinning of the second plans
1.6.2. Setting of the first plans
1.6.3. Finishing and polishing
D. DECORATIVE COVERINGS IN METAL LEAFS AND POLYCHROMES
1. Art and technique of gilding and silvering
1.1. Materials and preparatory techniques of wood surface
1.1.1. Wood preparation to receive the layers
1.1.2. The preparatory or bedding layers of the metal leaf
1.1.3. Levelling and polishing the preparation layers
1.2. Materials and techniques of fine gold and silver, and imitation leafs coatings
1.2.1. The water or tempera mordant
1.2.2. The oil or mordant
1.3. Types of finishes of metal coverings
1.3.1. Burnished, semi-matt, matte, frosted
1.3.2. Application of protection layer
2. Art and technique of polychromes on metal coverings
2.1. Upholstery imitation painting
2.2. Sgraffito
2.3. Punctured
E. DECORATIVE TECHNICAL IN FURNITURE
1. Art and technique of wood decorating and coating
1.1. Inlays
1.2. Wood Plating, veneers and marquetry
1.3. Encrusted
2. Art and technique of wood colouring
2.1. Colouring with aqueous wood stains
2.2. Colouring with transparency dyes
3. Art and technique of woods finishings
3.1. Polishing with abrasives materials, dry polishing's, or preparatory polishing's
3.2. Polishing with cedar, linseed or teak oils
3.3. Polishing with liquid Vaseline
3.4. Polishing with waxes
3.5. The English polishing, half polishing with beeswax & shellac varnish, or Portuguese polishing
3.6. The French polishing, ethyl alcohol and shellac polishing, or rag-doll polishing
Evaluation Methodology
Acts of Integrated Evaluation and Their Weighting in the Continuous and Final Evaluation:
THEORETICAL COMPONENT:
-Portfolio Descriptive Memory (40%);
LABORATORY PRACTICE COMPONENT:
-Portfolio Exercises developed (50%);
-Attendance, participation and organization in classes (10%).
Additional information:
-The assessment results from the weighting of the assessment items of the theoretical component (Portfolio Descriptive Memory 40%) and the practical laboratory component (Portfolio Exercises developed; Attendance, participation and organization in classes 60%) with the student having to obtain, at least 10 values for each component to get approval;
-The students who have an average equal to or greater than 10 do not need to take the exam;
-Students who obtain at least 10 marks in the laboratory practical component will be admitted to the exam;
-Students who do not obtain at least 10 marks in the laboratory practical component will be excluded from the exam;
-Possible improvements will only be made to the theoretical component Descriptive memory the assessment obtained in the laboratory practical component being considered in the final global weighting.
Bibliography
- BAUDRY, M. (1978). La Sculpture. Paris: Ministére de la Culture, Imprimerie National
- BROUN, J. (1994). The Encyclopedia of Wood Working Techniques. London: Quatro Publishing, Headline Book Publishing
- TRILLAT, R. e AIMPEAU, B. e TRILLAT, H. (1981). Technologie des Métiers du Bois: Menuiserie, Ebénisterie, Agencement. (Vol. 1,2,3). Paris: Dunod
(1991). Gilded Wood: Conservation and History. (Gilding Conservation Symposium, Philadelphia Museum of Art, Pennsylvania). Madison, Connecticut: Sound View Press
Teaching Method
1.Theoretical classes, of an expository nature
2. Laboratory Practical Classes, practical application sessions where exercises are developed from the design phase to the finish
3. Tutorial guidance, pedagogical, technical & scientific support.
Software used in class
Not applicable.