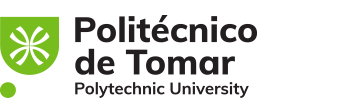
Publication in the Diário da República: Despacho nº 3359/2013 - 01/03/2013
7 ECTS; 1º Ano, 1º Semestre, 30,0 T + 60,0 PL + 6,0 OT , Cód. 964443.
Lecturer
- Regina Aparecida Delfino (1)(2)
- Vitor Dinis Carita de Jesus (2)
- Paula Alexandra Costa Leite Pinto Pereira (2)
(1) Docente Responsável
(2) Docente que lecciona
Prerequisites
Not applicable.
Objectives
THEORETICAL
Acquisition of knowledge of the stages that constitute the different workflows in the printing industry. Acquire general knowledge about originals and their reproductivity, typography and color.
Understanding the different graphic reproduction systems and their specific application. Acquire in-depth knowledge regarding the constitution of the printer form suitable for industrial production.
ENGRAVING
Theoretical knowledge of the different technical processes of engraving, and practical domain of the technical process of engraving in etching.
TYPSETTING
Acquisition of theoretical-practical knowledge related to typsetting in manual composition. Know the typographic rules. To develop practical works in the workshop of manual composition thus providing experimentation with types and graphic composition.
Program
THEORETICAL
1. Graphic production flow (prepress, printing and postpress)
2. Originals [text: fonts / image: dash-line, continuous tone, discontinuous tone (reticles)]
3. Color composition [additive synthesis (RGB), subtractive synthesis (CMYK) and direct colors (Pantone)
4. Graphic and reproducibility
5. Definition of the printing processes (ISO standards) through forms (analog / digital), and by system
5.1. Relief Forms (typography and flexographic)
5.2. Planographic forms (offset)
5.3. Recess Forms (gravure and pad printing)
5.4. Permeographic forms (serigraphy)
6. Digital Printing
7. Comparison between printing processes
ENGRAVING
1. Theoretical knowledge of the different Technical Processes of relief
1.1. Woodcut
1.2. Linogravura
1.3. Matrices and tools to be used
1.4. Graphic suitable for these techniques
2. Theoretical knowledge of the different Technical Processes of planographic engraving
2.1. Lithographic
2.2. Matrices and tools to be used
2.3. Graphics suitable for this technique
3. Theoretical knowledge of the different Technical Processes of recess
3.1. Technical processes of direct intervention recess
3.1.1. Dry tip
3.1.2. Carve candy
3.1.3. Mezzotint (the black way)
3.2. Technical Processes of indirect intervention recess
3.2.1. Etching
3.2.2. Water-ink
3.2.3. Soft varnish
4. Practical etching exercises
4.1. Preparation of matrices. Rounding of the corners and bevelling of the edges of the matrix
4.1.2. Polishing of matrices
4.1.3. Preparation of matrices with Jewish Bitumen
4.1.4. Passage and opening of the graphism in the matrix
4.1.5. Acid bath for opening the bite
4.1.6. Cleaning of the matrix
4.2. Printing proofs of status
4.2.1. Roles and inks to use. Importance of ink dilution
4.2.2. Pressure tests on the press
4.3. Printing of proofs of author
4.3.1. Cleaning and finishing of the tests
4.3.2. Unit correction
TYPSETTING
1. Presentation of the typographic composition sector
1.1. Furniture; utensils, presses
1.2. Knowledge of metallic materials and metal alloys
1.3. Typographic Boxes
2. Typography
2.1. Typometry (Didot and Anglo-American System)
2.2. Typology: Classification as Family, Form, Spelling and Series
2.3. Classification by family: Morphological Decimal of G. Pelliteri (National Press)
3. Composition styles. Paragraph break
4. Press conferences
5. Review of evidence
6. Printing of final proof in press
7. Distribution of types
8. Mechanical composition: Monotype and Linotype
9. Photocomposition
Evaluation Methodology
Continuous assessment
THEORETICAL: (33,33%). Written test: 90% and Participation in the Technical Conferences/Report: 10%.
LABORATORY PRACTICES (P/L). ENGRAVING (33,33%) Practical assignment: 95% and class attendance: 5%. TYPESETTING (33,33%) Practic
Bibliography
- BAER, L. (2005). Produção Gráfica. São Paulo: Editora Senac
- BAGILHOLE, R. (1996). Guia prático de Gravura. Lisboa: Editorial Estampa
- BARBOSA, C. (2009). Manual de Produção Gráfica. Parede: Principia
- CATAFAL, J. e OLIVA, C. (2003). A Gravura. Lisboa: Editorial Estampa
- DAWSON, J. (1982). Guia completo de grabado e impressión - Técnicas y materiales. Barcelona: H. Blume Ediciones
- DIAS, R. e MEIRA, S. (2018). Imprimere: arte e processo nos 250 anos da Imprensa Nacional. . Lisboa: INCM, ESAD
- HEITLINGER, P. (2006). Tipografia, origens, formas e uso das letras. Lisboa: Dinalivro
- JOHANSSON, K. e LUNDBERG, P. e RYBERG, R. (2004). Manual de producción gráfica. Recetas.. Barcelona: Editorial Gustave Gili
- KIPPHAN, H. (2001). Handbook of print media: technologies and production methods. Heidelberg: Springer
- VILELA, A. (1978). Cartilha das Artes Gráficas. Braga: STGRAMINHO
Teaching Method
1.Presentation of theoretical contents using audiovisual resources. Discussion/analysis and comparison of printed items.
2.Field trip
3.Engraving: practical projects with etching.
4.Typesetting: hand setting exercises.
Software used in class
Not applicable.