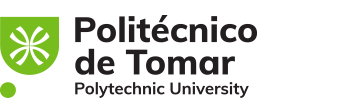
Publication in the Diário da República: Despacho n.º 10852/2016 - 05/09/2016
4 ECTS; 3º Ano, 1º Semestre, 15,0 T + 30,0 PL + 2,0 OT , Cód. 938069.
Lecturer
- Fernando dos Santos Antunes (1)(2)
(1) Docente Responsável
(2) Docente que lecciona
Prerequisites
Not applicable.
Objectives
Knowledge of the techniques and technologies of wood carving and furniture artistic production;
Knowledge/use of raw materials, products, materials, tools and equipment;
Put into practice the main production techniques;
Develop manual skills, concentration and technical accuracy in execution.
Program
A.INTRODUCTION TO THE HISTORY OF WOODCARVING AND FURNITURE
B.INTRODUCTION TO WOOD LABORATORY
1.Principal equipment and tools
2.Basic hygiene rules, health, safety and organization
C.MATERIALS APPLIED IN ARTISTIC PRODUCTION OF TIMBER ARTIFACTS
1.Terminology used in woodworking area
2.Types of woods
3.Types of resins, adhesives and gums
4.Types of metal leafs
D.WOOD STRUCTURES ASSEMBLAGE AND JOINERY SYSTEMS
«Art and technique of assemblage in wood objects»
1.Assemblage and joinery classification
1.1.The assemblage shapes
1.2.Types of assemblages
1.3.Types of joinery
1.3.1.Dovetails
2.Application in the artistic production of woodcarving and furniture
3.Production techniques of assemblages and joinery
3.1.Selection and preparation of wood
3.2.Measurement
3.3.Draw cutting lines
3.4.Cutting and setting
4.Collage and clamping techniques
4.1.Types of adhesives and clamping tools
E.ORNAMENTAL AND FIGURATIVE DECORATIVE TECHNIQUES
«Art and technique of carving or sculpting wood objects»
1.Materials and techniques
1.1.Execution of drawing or sketch and auxiliary markings
1.2.The selection and preparation of wood
1.3.Transposition of the drawing
1.4.Cut out the contours
1.5.Wood thinning
1.6.Modelling of volumes
1.6.1.Thinning of the second plans
1.6.2.Setting of the first plans
1.6.3.Finishing and polishing
F.DECORATIVE COVERINGS IN METAL LEAFS AND POLYCHROMES
«Art and technique of gilding and silvering»
1.Materials and preparatory techniques
1.1.Wood preparation to receive the layers
1.2.The preparatory or bedding layers of the metal leaf
1.2.1.Animal glue
1.2.2.White preparation
1.2.3.Armenian clay "bollus"
1.3.Levelling and polishing the preparation layers
2.Materials and techniques of gold and silver, and imitation leafs coatings
2.1.The water or tempera mordant
2.2.The oil or mordant
3.Types of finishes of metal coverings
3.1.Burnished, semi-matt, matte, frosted
3.2.Application of protection layer
«Art and technique of polychrome on metal coverings»
4.Materials and techniques of polychromes
4.1.Upholstery imitation painting
4.2.Sgraffito
4.3.Punctured
G.DECORATIVE TECHNICAL IN FURNITURE
«Art and technique of wood decorating and coating»
1.Materials and decorative techniques
1.1.Inlays
1.2.Wood Plating, veneers and marquetry
1.3.Encrusted
«Art and technique of colouring»
2.Colouring with aqueous wood stains
2.1.Wood powder mordants oak, walnut, mahogany, teak, ebony and palisander
3.Colouring with transparency dyes
3.1.Water anilines and alcohol anilines
«Art and technique of woods finishing»
4.Materials and techniques in furniture polishing
4.1.Polishing with abrasives materials, dry polishing's, or preparatory polishing's
4.2.Polishing with cedar, linseed or teak oils
4.3.Polishing with liquid Vaseline
4.4.Polishing with waxes
4.5.The English polish, half polishing with bees wax & shellac varnish, or Portuguese polish
4.6.The French polish, alcohol spirit and shellac polish, or Rag-doll polish
Evaluation Methodology
Assessment and weighted average:
Theoretical component:
-Portfolio descriptive report (40%)
Practical component:
-Portfolio exercises (50%)
-Assiduity, commitment and organization in the class (10%).
Additional information:
-The students are obliged to comply with all assessment items, being able to choose to be globally assessed in continuous assessment, or in final assessment;
-The students, to be admitted to the final evaluation, must have a positive evaluation of the laboratory practical component, with a minimum of 9.5 values, in continuous evaluation;
-the students will be able to submit the written works of the theoretical component in final evaluation - exam period;
-Eventual improvements will be made only to the theoretical component - written works - being considered in the final global weighting the evaluation obtained in the laboratory practical component.
Bibliography
- BAUDRY, M. (1978). La Sculpture. Paris: Ministére de la Culture, Imprimerie National
- BROUN, J. (1994). The Encyclopedia of Wood Working Techniques. London: Quatro Publishing, Headline Book Publishing
- TRILLAT, R. e AIMPEAU, B. e TRILLAT, H. (1981). Technologie des Métiers du Bois: Menuiserie, Ebénisterie, Agencement. (Vol. 1,2,3). Paris: Dunod
(1991). Gilded Wood: Conservation and History. (Gilding Conservation Symposium, Philadelphia Museum of Art, Pennsylvania). Madison, Connecticut: Sound View Press
Teaching Method
Continuous Assessment: students will perform different optional exercises from the phase of design to the selection and preparation of woods,the marking and transposition of drawing/sketch, the woodworking and decoration/finish.
Software used in class
Not applicable.