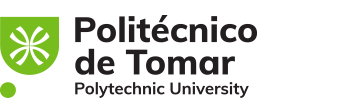
Publication in the Diário da República: Despacho nº 1469/2007
5 ECTS; 2º Ano, 2º Semestre, 15,0 T + 30,0 TP + 15,0 TC + 3,50 OT , Cód. 912320.
Lecturer
- Teresa Leonor Ribeiro C. M. Morgado (2)
(1) Docente Responsável
(2) Docente que lecciona
Prerequisites
Prior knowledge of statistics and reliability
Objectives
Ministering to the students knowledge of Maintenance Management. Equip students with tools capable of organizing and / or managing a maintenance department.
Program
1. Introduction to Industrial Maintenance:
1.1. Definition of Maintenance;
1.2. Function Maintenance Industry
1.3. Objectives of a Maintenance Organization;
1.4. Functional organization chart of the Organization of Maintenance Service
1.5. Types of maintenance;
1.6. Times relating to maintenance;
1.7. Reliability Maintainability, Availability;
1.8. Different forms of maintenance: Curative Maintenance and Preventive Maintenance;
1.9. Other activities Maintenance Service;
1.10. Selecting the type of maintenance to use.
2. Equipment of knowledge:
2.1. Nature and Equipment Classification;
2.2. Analyse Equipment levels;
2.3. History equipment.
3. Behavior of goods or equipment:
3.1. Definition of damage;
3.2. Study of a system;
3.3. Damage rates;
3.4. Exploitation of damage reports;
3.5. Pareto diagrams;
3.6. Systems Reliability curve.
4. Centered Maintenance Reliability:
4.1. Definition of reliability;
4.2. Definition of failure;
4.3. Intrinsic and extrinsic reliability;
4.4. Reliability requirements;
4.5. Lifecycles of an organ;
4.6. Steps Reliability;
4.7. Measurement Reliability;
4.8. Mortality curve (or survival);
4.9. Common statistical distributions to represent the expected life;
4.10. Size of a sample, test time, confidence level.
5. Maintainability and Availability:
5.1. Definition of maintainability;
5.2. Repair Technicians times;
5.3. Notion of availability;
5.4. Model Availability;
5.5. Predictive reliability.
6. Analysis of Maintenance Costs:
6.1. Importance of cost analysis;
6.2. Direct and indirect costs;
6.3. Amortization Analysis Model;
6.4. Different costs depending on the type of maintenance.
7. Preparation of Maintenance Actions:
7.1. Criticality table of equipment;
7.2. Use of an ABC curve;
7.3. Preparation of Corrective Maintenance;
7.4. Preparation of Palliative maintenance;
7.5. Preparation of repair works;
7.6. Preventive Actions of preparation;
7.7. Preparation of Ronda maintenance;
7.8. Preparation of Systematic Maintenance;
7.9. Preparation of the Conditional Maintenance.
8. Function Planning:
8.1. The five planning levels;
8.2. Specific character of the maintenance work planning;
8.3. Procedures Relating to Maintenance Work.
9. Maintenance Service Management:
9.1. Iterative Model Management;
9.2. Management Indicators description;
9.3. Replacement Parts Inventory Management;
9.4. Spent Frequent parts management;
9.5. Parts Management "Security";
9.6. Maintenance and Foreign Markets.
10. The maintenance policy:
10.1. Choice of Technical Economic Objectives;
10.2. Choose Maintenance Method to Apply;
10.3. Optimization of Preventive level to be used;
10.4. Repairable equipment;
10.5. Optimization replacement period;
10.6. Equipment replacement;
10.7. Possession cost of equipment.
Evaluation Methodology
Two written tests (75%) and fieldwork report (s) (25%)
Written assessment includes tests and/or exams. A minimum of 7.0 is required in the written test
Bibliography
- Ferreira, L. (1998). Uma introdução à manutenção. (Vol. .). (pp. 1-193). Portugal: Publindústria
Teaching Method
Lectures and theoretical-practical sessions with content presentation and resolution of worksheets. Fieldwork classes include on-site visits to industry and workshops with Maintenance Engineer as a guest speaker.
Software used in class
Excel